Solar Power 24/7 with
Thermal Energy Storage
Molten salt was initially identified as a working and storage fluid for concentrating solar power (CSP) power tower plants by Sandia National Laboratories as early as the mid-1970s. An extensive review of potential materials led ultimately to the selection of two materials, a molten nitrate salt and liquid sodium, for follow-up and system development.
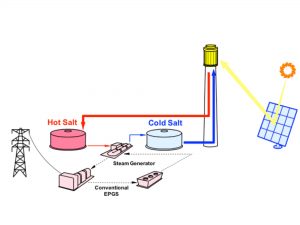
Sodium, while an excellent heat transfer fluid, had no real potential as a storage medium and was ultimately rejected on the basis of safety. The molten nitrate salt mixture, 60wt% NaNO3 and 40wt% KNO3 (similar to commercial draw salt, and called “solar salt” herein), became the preferred solution based on melting and freezing points covering the desired range of operating temperatures, stability in air at temperatures up to 600ºC, heat transfer and heat capacity properties, safety, availability, and cost.
The potential for improving the impact of CSP through storage (providing dispatchable power and lower cost) led to development of the 10-MWe Solar Two Pilot Plant, built and tested in the 1990s. Solar Two successfully proved the potential of the technology and identified design enhancements to improve performance, reliability, and cost.
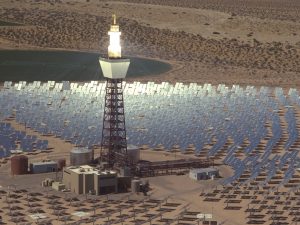
The success of Solar Two led to use of MS-based storage in commercially proven parabolic trough plants, but more importantly, to large-scale power towers based directly on the Solar Two design. Parabolic trough technology, because of its low concentration ratios (typically below 100) is limited in operating temperature to about 400ºC. Power towers operate at much higher concentration ratios (potentially well above 1000°C), and thus can be efficient at temperatures up to 800ºC and higher. Nitrate salt stability, however, imposes an upper limit of 565ºC, adequate for modern steam cycles, but inadequate for the higher temperature capabilities of advanced power cycles such as supercritical CO2 cycles.
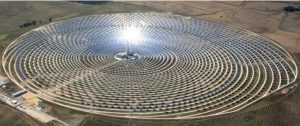
The first near-commercial power tower plant utilizing MS storage was the 20-MWe Gemasolar plant developed by Sener/Torresol in Andalucía, Spain. Gemasolar has operated successfully since 2011, demonstrating 24/7 operation at full power during good summer solar conditions.
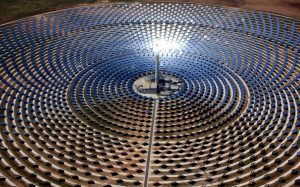
The first (and so far only) large, truly commercial-scale power tower plant based on Solar Two technology, the 110-MWe Crescent Dunes plant, was built by SolarReserve in Tonopah, NV. With 10 hours of storage, it delivers power 24/7 in the summer to the Nevada grid.
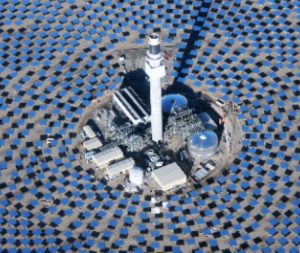
Smaller power tower plants (10-15 MW) have the potential for application in desalination or enhanced oil recovery, and in off-grid settings.
Note that even with storage, CSP is not always available truly “on demand.” In a typical “maximum storage” (75% capacity factor) design, power can be available 24/7 during summer months, as long as the sun is shining consistently. With cloudy weather, availability is, of course, lessened (and even the best sites have a significant amount of poor solar availability), and typically drops to 50% or less in winter months because of the shorter days. Bottom line: MS storage systems can provide hours of storage, but not enough to get through significant weather outages and certainly not seasonal storage.
Nearly 2 GW of molten nitrate salt plants are in operation or under construction around the world.
Cost Implications of Molten Salt CSP Storage.
To understand the economics of a CSP plant with MS storage, think of a large power tower plant without storage, and with a power block (steam generator, steam turbine/generator, etc.) large enough to accommodate peak solar output of the plant. (Note that the power block would sit unused half the year (nights), and would be somewhat underutilized much of the year when solar conditions were not at their peak).
Now think of doubling the solar capacity. One way to accommodate that would be to install a second power block (doubling the power block cost).
Another would be to double the power block size (which wouldn’t double the power block cost, but would increase it by perhaps 65% (based roughly on a 0.7 power law estimate for scaling turbine/generator costs)).
Another way to accommodate the additional solar energy would be to add MS storage to hold that additional thermal energy for use at times the power block was not otherwise fully utilized — cloudy weather and nights, for example. If the cost of the storage were less than the incremental cost of increasing the power block size, the levelized cost of energy (LCOE) from the plant would be less for the storage option. Such is actually the case for MS power towers with nitrate salt storage.
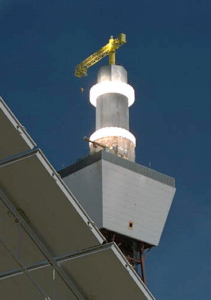
Note, too, that plant economics can be helped in other ways by MS storage systems. Plant operations can be simplified and efficiency
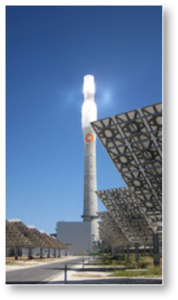
improved by always running the power block at full power (avoiding transients and off-design operation), as well as having more efficient receiver operation through solar transients (compared to, say, a water/steam receiver, which will drop offline during a cloud outage and require significant time to bring back on line). More importantly in many cases, storage can provide a significant increase in value of the power generated if power delivered dispatchably or during high demand periods when there is no sun — think evenings in the Southwest U. S. — is more valuable to the customer than power delivered, say, in the mornings.
Relative to the potential of other currently available salt options, limitations on peak system temperature resulting from salt instability (for nitrites and calcium nitrates, for example) would result in lower power block efficiencies as well as higher storage costs because of decreased temperature differentials. Use of more expensive salts (LiNO3 costing up to 10 times NaNO3, for example) would also change the storage cost balance from positive to negative.
Current technology, as implemented at Solar Two and Crescent Dunes for example, has an upper temperature limit of about 565ºC, which translates into maximum power cycle efficiency, utilizing a conventional steam turbine, of about 42%.
In contrast, the potential exists for use of advanced molten salts, stable at temperatures of up to 780°C, coupled with advanced alloys suitable for use in receivers, piping, storage systems, and heat transfer equipment. Advanced power tower plants based on these higher temperatures would have the potential to decrease costs by up to 15% or more, while maintaining the ability to generate power around the clock. This is our vision for the future of solar energy!
Molten Salt System Design Characteristics
In a power tower, the molten salt serves as both the working fluid and the storage fluid. “Cold” salt (285ºC, for example, for a nitrate salt system) is pumped from the cold storage tank to the receiver, where it is heated to maximum operating temperature (about 565ºC for nitrate salt systems). This “hot” salt is then returned to the hot storage tank. When needed for power production, hot salt is then pumped to a heat transfer system to heat the working fluid for the power generation system. (For a nitrate salt system, the heat transfer system is a MS steam generator, producing 550ºC steam to drive a conventional reheat steam turbine.) Cold salt exiting the steam generator is returned to the cold tank to repeat the process.
Key issues for major plant systems include the following:
Receivers are typically salt-in-tube designs, meaning the salt flows through vertical tubes arranged in panels and exposed to concentrated solar flux. The salt is heated to full operating temperature in one or more passes through the flux. Panel design and tube materials must account for temperatures as much as 100ºC above maximum salt working temperature; significant panel expansion (and differential expansion of tubes within a panel); corrosion effects of the salt on all containment materials; and perhaps most important of all, the low-cycle fatigue stresses induced in the panel during daily (and cloud transient-induced) thermal cycling of the receiver. High-nickel alloy materials (such as Inconels and Haynes materials) are typically required for nitrate salt systems, but innovative approaches will be required for our proposed higher-temperature systems.
MS storage systems are typically composed of large “hot” and “cold” tanks. These two-tank molten salt storage systems have consistently demonstrated average annual thermal efficiencies of about 99%. This is largely because the design temperatures of the storage system were chosen to match very closely the requirements of steam needed for modern steam turbines. Because of the very large sizes of these systems, losses are limited to the relatively small thermal losses associated with the tank walls and related system piping and pumping losses associated with pumping salt into and out of the tanks.
For example, a 50% capacity factor, 100-MWe nitrate salt power tower plant would require roughly 15000 to 20000 metric tonnes of salt, a 75% capacity factor plant up to 35000 tonnes. To accommodate this much salt, the hot and cold storage tanks at Crescent Dunes are, for example, each over 12m tall and over 40m in diameter. At Abengoa’s Solana trough plant, there are six each hot and cold tanks instead of a single tank for each temperature.
The “cascading tank” alternative has been looked into as an alternative to the commonly deployed two-tank arrangement.
Modular Storage Systems: Earlier on, our team developed a design for a modular thermal energy storage system that enables low-cost thermal storage for utility procurement in the range of 30-50 MWe . Our innovation will transform energy storge systems from high-cost and labor-intensive field assembled tanks to low-cost factory assembled integrated modules. We will leverage high volume manufacturing and factory assembly to dramatically reduce installed costs of thermal energy storage.
In this design, a number of 6- to 30-m3 factory-manufactured and -insulated tanks are cascaded in series (essentially functioning like a single thermocline tank, but without the efficiency losses of a thermocline) to provide both hot and cold salt storage. Storage size could thus be scaled effectively from about 1 MWh up to whatever is required, simply by increasing the number of tanks.
Such a cascading design might well lend itself better to higher-temperature systems than large two-tank systems.
Potential for Higher Temperature Systems. The above systems are based on nitrate salts and have an upper temperature limit of about 565ºC or less. Because the efficiency of power cycles increases with increasing temperature, especially when a SCO2 Brayton Cycle is used for power generation, there have long been efforts to develop higher temperature systems, which is the focus of our effort.
Pushing temperatures above 600-650ºC, for example, would allow use of the most efficient modern steam turbines (operating at 585ºC or so), temperatures up to 800ºC would allow use of Stirling engines (typically in parabolic dish systems), and temperatures above 900-1000ºC could theoretically allow use of Brayton or combined cycles. We are focused primarily on employing chloride salts to achieve operating temperatures up to 780ºC, which would allow integration with emerging supercritical CO2-based power conversion systems.
Selection of optimal salts for High-Temperature
MS storage
Cost is fundamentally the biggest driver in salt selection, at least for commercial systems. For tower systems, having a low-cost storage system can actually lower the LCOE from the plant, relative to not having storage (that is, the cost of storage can be less than the incremental cost of a larger power block to handle incremental additions to solar capacity). However, since storage can also add value to produced power (through dispatchability and/or time of day delivery), storage can also be desirable even if it drives up LCOE incrementally. Such is the case with trough systems where the lower differential temperature requires several times more salt for a given MWh capacity.
An example of the importance of even small cost changes as a driver in salt selection is solar salt. While the freezing point of the nitrate salt mixture could be reduced slightly by using the NaNO3/KNO3 eutectic (about 50/50), solar salt is specified as 60/40 because NaNO3 is approximately 30% cheaper than KNO3. A more extreme case is the potential use of LiNO3 to reduce the salt freezing point to about 120ºC by using about 30% LiNO3; since lithium nitrate can cost upwards of an order of magnitude more than NaNO3, it is not at all practical from a cost perspective.
Bottom line: it has been said that the storage material must be “cheaper than dirt” – basically possible if the salt is mined material, but hard to achieve otherwise.
Availability of the MS in large quantities is commercially critical. Nitrates are mined materials (although now are also produced synthetically from carbonates), typically used in huge quantities as fertilizers. Thus the industry is in place and sufficiently large to support massive CSP development with storage. A good counter example is lithium nitrate, which, while an excellent ternary additive to reduce the freezing point without impacting high temperature stability, is in much shorter supply and much more costly.
Freezing Point is another critical factor in salt selection. An ideal material would not freeze, even at a low ambient temperature, although no such practical salt is available. While the 240ºC freezing point of solar salt requires significant efforts in heat trace throughout a plant, this is workable with only minor impacts on cost. The freezing point also must be well below the lower working limit of the power cycle. The current system design of typical tower and trough systems use a reheat Rankine steam cycle with a low-side temperature of about 285°C. If the system used another power cycle (e.g., supercritical CO2) with higher upper and lower temperature limits, a higher freezing point might be acceptable (subject to heat trace and materials compatibility considerations).
High-Temperature Stability of the salt is important in matching the high temperature of the power cycle used. The 565ºC bulk temperature limit on solar salt, for example, is a good match to all but the most state-of-the art reheat steam turbines (although 600-620ºC would be slightly better for the newest 585ºC steam turbines). As noted above, chloride-based salts with stability up to 780ºC could offer significant efficiency advantages by matching the temperature range of an appropriate power cycle and appropriate containment materials.
Corrosivity and Compatibility with Vessel and Piping Containment Materials is another issue. As discussed above, nitrate and nitrite materials are compatible with common steels and stainless steels at typical solar operating conditions, and thus not a problem. Our research indicates that the chlorides and other potentially higher temperature materials would have to be very carefully evaluated and tested to assure compatibility with process equipment and material selections. While some ceramics have potential as containment materials, ceramic brittleness and lack of readily available connection approaches (like welding for metals) make their use challenging.
Thermal Properties can impact application choices as well, although generally to a lesser extent. Nitrates have a heat capacity of around 1500 J/kg.K, so the details of nitrate selection do not depend significantly on heat capacity. According to prior studies, the chloride-based salts have a heat capacity of about half that of nitrates, so all other things being equal, costs could be higher using chlorides to achieve higher temperatures. Finally, thermal conductivity can significantly impact receiver and steam generator design. In this regard, nitrates (about 0.5 W/m.K) are not really very good (liquid sodium, for example, is two orders of magnitude higher heat capacity (although it may be unsuitable from a safety perspective)). Most salts will likely be in the same range as nitrates (although data availability is limited).
Bottom Line. At the present time, industry uses solar salt (60wt% NaNO3, 40wt% KNO3) as the choice in the current fleet of commercial CSP storage systems. Nitrite-based materials (e.g., Hitec: 40wt% NaNO2, 7wt% NaNO3, 53wt% KNO3) could be suitable for lower temperature systems (up to about 450ºC), while chloride-based materials have future potential to be useful in higher temperature systems. The solar salt — and to a lesser extent nitrite-based materials — are very well understood for CSP applications. New materials for fabrication of the hot and cold tanks and the piping system and pumps, etc., along with the chloride salts, will require extensive testing and scaling up to industrial-scale testing and operation.
Our team and our demonstration facility intend to accomplish these tasks and to achieve the CSP industry commercial buy-in and use.